Order Products
Industries
Food & Beverage
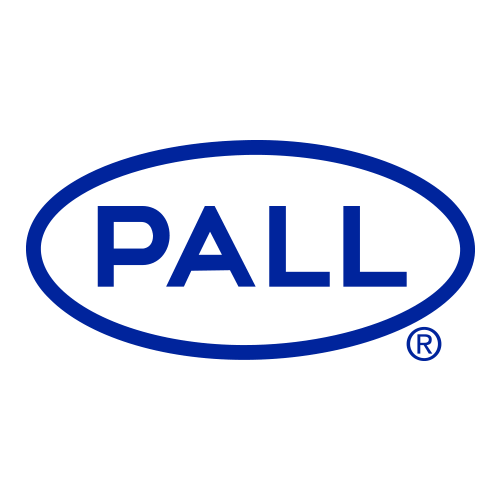
Filter 30" Fluorodyne II 0.1µm
1/EA
1
Emflon® PFRW Kleenpak™ Capsules, 0.2µm, 158 mm,
1/EA
1
Emflon® PFRW Kleenpak™ Capsules, 0.2µm, 174 mm,
1/EA
1
Emflon® PFRW Junior Style Filter Cartridge, 0.2µm, 5.3 in, Internal Plug seal with single 116 Silicone Elastomer O-ring
1/EA
1
Emflon® PFRW Filter Cartridge, 0.2µm, 5 in, Single open ended Code 2, Silicone Elastomer O-ring
1/EA
1
Emflon® PFRW Filter Cartridge, 0.2µm, 10 in, Single open ended Code 7, Silicone Elastomer O-ring
1/EA
1
Junior Filter Emflon PFR 0.2µm
1/EA
1
Ultipor® N66 Filter Cartridges, Nylon Hardware, 0.45 µm single layer, 30 in, Single Open Ended Code 7, Silicone Elastomer O-ring
1/EA
1
Profile® II Filter Cartridges, 0.5 µm, 40 in, Single Open Ended Code 7, Silicone Elastomer O-ring
1/EA
1
SUPRAdisc SD II 080 200X080C232SPW
1/EA
1